Biffa Insights
Home for thought leadership, news, case studies and more.
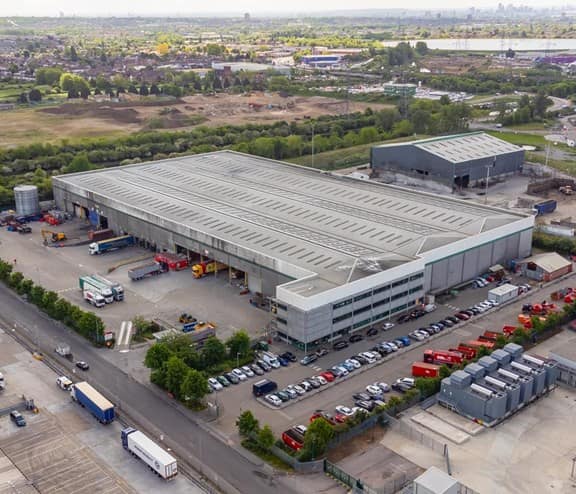
Biffa’s emissions targets validated by Science Based Targets initiative
Biffa has announced that its near-term scope 1, 2 and 3 emissions targets have been validated by the Science Based Targets initiative (SBTi).